Cel materiałów powłokowych
Powlekanie zewnętrznej powierzchni rur stalowych jest kluczowe, aby zapobiec rdzewieniu. Rdzewienie na powierzchni rur stalowych może znacząco wpłynąć na ich funkcjonalność, jakość i wygląd wizualny. Stąd proces powlekania ma znaczny wpływ na ogólną jakość produktów rur stalowych.
-
Wymagania dotyczące materiałów powłokowych
Zgodnie z normami ustalonymi przez American Petroleum Institute, rury stalowe powinny być odporne na korozję przez co najmniej trzy miesiące. Jednak zapotrzebowanie na dłuższe okresy antykorozyjne wzrosło, a wielu użytkowników wymaga odporności przez 3 do 6 miesięcy w warunkach przechowywania na zewnątrz. Oprócz wymogu trwałości użytkownicy oczekują, że powłoki utrzymają gładką powierzchnię, równomierne rozłożenie środków antykorozyjnych bez żadnych przeskoków lub kapania, które mogłyby wpłynąć na jakość wizualną.
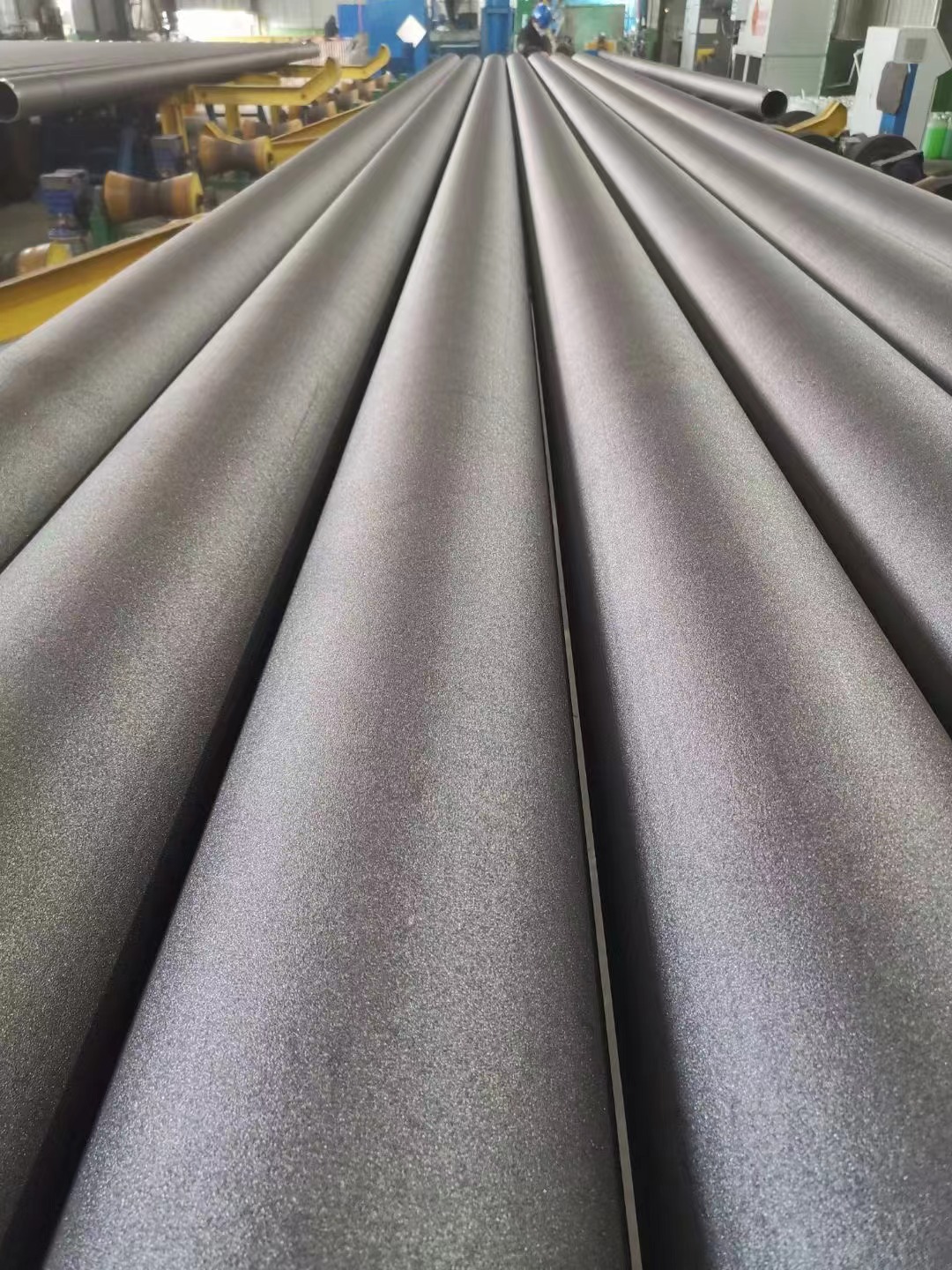
-
Rodzaje materiałów powłokowych i ich zalety i wady
W miejskich sieciach rurociągów podziemnychrury stalowesą coraz częściej używane do transportu gazu, ropy, wody i innych. Powłoki tych rur ewoluowały od tradycyjnych materiałów asfaltowych do materiałów z żywicy polietylenowej i żywicy epoksydowej. Stosowanie powłok z żywicy polietylenowej rozpoczęło się w latach 80. XX wieku, a wraz z różnymi zastosowaniami komponenty i procesy powlekania stopniowo się poprawiały.
3.1 Powłoka z asfaltu naftowego
Powłoka z asfaltu naftowego, tradycyjna warstwa antykorozyjna, składa się z warstw asfaltu naftowego, wzmocnionych tkaniną z włókna szklanego i zewnętrzną ochronną folią z polichlorku winylu. Zapewnia doskonałą wodoodporność, dobrą przyczepność do różnych powierzchni i opłacalność. Ma jednak wady, w tym podatność na zmiany temperatury, staje się krucha w niskich temperaturach i jest podatna na starzenie i pękanie, szczególnie w warunkach skalistego podłoża, co wymaga dodatkowych środków ochronnych i zwiększa koszty.
3.2 Powłoka epoksydowa na bazie smoły węglowej
Epoksyd z smoły węglowej, wykonany z żywicy epoksydowej i asfaltu smołowego, wykazuje doskonałą odporność na wodę i chemikalia, odporność na korozję, dobrą przyczepność, wytrzymałość mechaniczną i właściwości izolacyjne. Wymaga jednak dłuższego czasu utwardzania po aplikacji, co czyni go podatnym na niekorzystne skutki warunków atmosferycznych w tym okresie. Ponadto różne składniki stosowane w tym systemie powłok wymagają specjalistycznego przechowywania, co podnosi koszty.
3.3 Powłoka proszkowa epoksydowa
Powłoka proszkowa epoksydowa, wprowadzona w latach 60. XX wieku, obejmuje elektrostatyczne natryskiwanie proszku na wstępnie obrobione i podgrzane powierzchnie rur, tworząc gęstą warstwę antykorozyjną. Jej zalety obejmują szeroki zakres temperatur (od -60°C do 100°C), silną przyczepność, dobrą odporność na odspojenie katodowe, uderzenia, elastyczność i uszkodzenia spoin. Jednak cieńsza warstwa sprawia, że jest podatna na uszkodzenia i wymaga zaawansowanych technik produkcji i sprzętu, co stwarza wyzwania w zastosowaniach terenowych. Chociaż pod wieloma względami przewyższa polietylen, pod względem odporności na ciepło i ogólnej ochrony przed korozją wypada słabo w porównaniu z polietylenem.
3.4 Powłoka antykorozyjna z polietylenu
Polietylen oferuje doskonałą odporność na uderzenia i wysoką twardość, a także szeroki zakres temperatur. Znajduje szerokie zastosowanie w zimnych regionach, takich jak Rosja i Europa Zachodnia, w rurociągach ze względu na swoją doskonałą elastyczność i odporność na uderzenia, szczególnie w niskich temperaturach. Jednak nadal istnieją wyzwania w jego stosowaniu w rurach o dużej średnicy, gdzie mogą wystąpić pęknięcia naprężeniowe, a wnikanie wody może prowadzić do korozji pod powłoką, co wymaga dalszych badań i udoskonaleń w zakresie materiałów i technik aplikacji.
3.5 Gruba powłoka antykorozyjna
Ciężkie powłoki antykorozyjne zapewniają znacznie zwiększoną odporność na korozję w porównaniu ze standardowymi powłokami. Wykazują długoterminową skuteczność nawet w trudnych warunkach, a ich żywotność przekracza 10 do 15 lat w środowiskach chemicznych, morskich i rozpuszczalnikowych oraz ponad 5 lat w warunkach kwaśnych, zasadowych lub solnych. Te powłoki mają zazwyczaj grubość suchej warstwy od 200 μm do 2000 μm, co zapewnia doskonałą ochronę i trwałość. Są szeroko stosowane w konstrukcjach morskich, sprzęcie chemicznym, zbiornikach magazynowych i rurociągach.
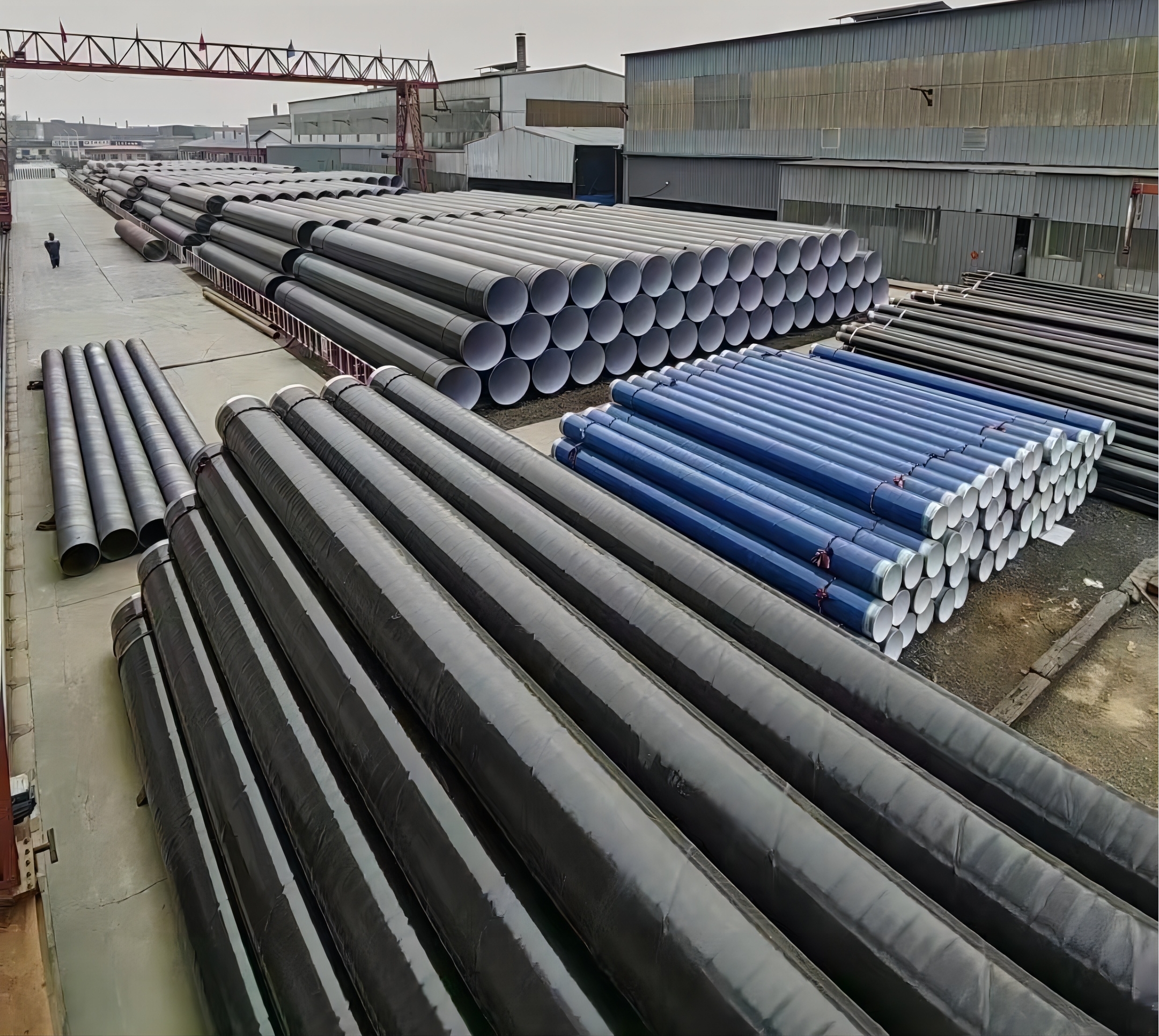
-
Typowe problemy z materiałami powłokowymi
Do typowych problemów z powłokami zalicza się nierównomierne nakładanie, kapanie środków antykorozyjnych i tworzenie się pęcherzyków.
(1) Nierównomierna powłoka: Nierównomierne rozłożenie środków antykorozyjnych na powierzchni rury powoduje powstawanie obszarów o nadmiernej grubości powłoki, co prowadzi do strat, natomiast cienkie lub niepokryte obszary zmniejszają właściwości antykorozyjne rury.
(2) Kapanie środków antykorozyjnych: Zjawisko to polega na tym, że środki antykorozyjne krzepną na powierzchni rury i przyjmują kształt kropli, co wpływa na estetykę, nie wpływając bezpośrednio na odporność na korozję.
(3) Tworzenie się pęcherzyków: Powietrze uwięzione w środku antykorozyjnym podczas aplikacji tworzy pęcherzyki na powierzchni rury, co wpływa zarówno na wygląd, jak i skuteczność powłoki.
-
Analiza problemów z jakością powłok
Każdy problem powstaje z różnych przyczyn, jest spowodowany przez różne czynniki; a wiązka rur stalowych wyróżniona przez jakość problemu może być również kombinacją kilku. Przyczyny nierównomiernego powlekania można z grubsza podzielić na dwa rodzaje, jednym jest nierównomierne zjawisko spowodowane natryskiwaniem po wejściu rury stalowej do skrzynki powlekającej; drugim jest nierównomierne zjawisko spowodowane brakiem natryskiwania.
Powód pierwszego zjawiska jest oczywisty i łatwy do zauważenia, w przypadku sprzętu do powlekania, gdy stalowa rura do skrzynki powlekającej w zakresie 360° wokół łącznie 6 pistoletów (linia obudowy ma 12 pistoletów) do natryskiwania. Jeśli każdy pistolet natryskiwany z wielkością przepływu jest inny, doprowadzi to do nierównomiernego rozprowadzenia środka antykorozyjnego na różnych powierzchniach stalowej rury.
Drugim powodem jest to, że istnieją inne przyczyny nierównomiernego powlekania oprócz czynnika natryskiwania. Istnieje wiele rodzajów czynników, takich jak rdza na rurach stalowych, szorstkość, przez co trudno jest równomiernie rozprowadzić powłokę; powierzchnia rury stalowej ma pomiar ciśnienia wody pozostawiony po emulsji, tym razem dla powłoki z powodu kontaktu z emulsją, przez co konserwant jest trudny do przyłączenia się do powierzchni rury stalowej, przez co nie ma powłoki części rury stalowej emulsji, co powoduje, że powłoka całej rury stalowej nie jest jednolita.
(1) Powód wiszących kropli środka antykorozyjnego. Przekrój poprzeczny rury stalowej jest okrągły, za każdym razem, gdy środek antykorozyjny jest rozpylany na powierzchnię rury stalowej, środek antykorozyjny w górnej części i krawędzi będzie płynął do dolnej części ze względu na czynnik grawitacji, co utworzy zjawisko wiszących kropli. Dobrą rzeczą jest to, że w linii produkcyjnej powłok fabryki rur stalowych znajdują się urządzenia piecowe, które mogą podgrzewać i utwardzać środek antykorozyjny rozpylany na powierzchni rury stalowej w czasie i zmniejszać płynność środka antykorozyjnego. Jednakże, jeśli lepkość środka antykorozyjnego nie jest wysoka; brak terminowego ogrzewania po rozpyleniu; lub temperatura ogrzewania nie jest wysoka; dysza nie jest w dobrym stanie technicznym itp. doprowadzi to do wiszących kropli środka antykorozyjnego.
(2) Przyczyny pienienia antykorozyjnego. Ze względu na wilgotność powietrza w miejscu pracy, dyspersja farby jest nadmierna, spadek temperatury procesu dyspersji spowoduje zjawisko pęcherzykowania środka konserwującego. Wilgotność powietrza, niższe warunki temperaturowe, środki konserwujące rozpylane z rozproszonego materiału w postaci drobnych kropelek doprowadzą do spadku temperatury. Woda w powietrzu o wyższej wilgotności po spadku temperatury będzie się skraplać, tworząc drobne kropelki wody zmieszane ze środkiem konserwującym, a ostatecznie przedostaną się do wnętrza powłoki, powodując zjawisko pęcherzykowania powłoki.
Czas publikacji: 15-12-2023